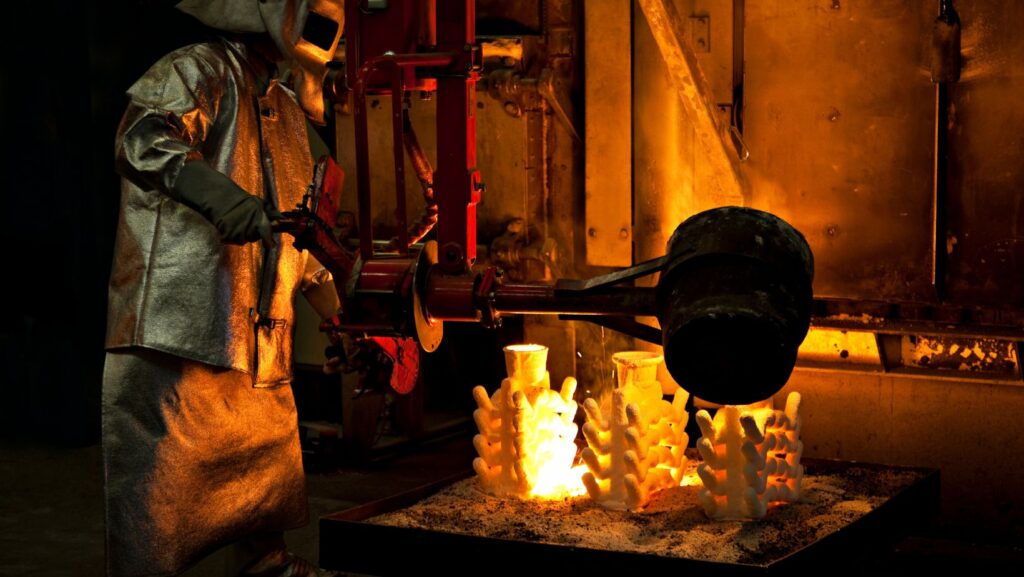
Precision casting techniques help make strong and long-lasting products. These methods shape metal with great accuracy. They allow for detailed designs and reduce material waste.
Industries use them to improve strength and reliability. Products made this way last longer under stress. They also resist damage from wear and tear.
Here are some ways to improve durability using precision casting techniques.
Selecting the Right Alloy for Strength
Choosing the right metal is important for product durability. Some alloys are stronger and more resistant to damage. High-quality metals ensure better performance under pressure.
Heat-resistant alloys work well in extreme conditions. Corrosion-resistant materials prevent rust and decay. The right combination increases longevity. Precision casting helps shape these materials without defects.
Improving Surface Finishing Techniques
A smooth surface improves durability and performance. Precision casting allows fine surface details. Polishing removes rough edges and weak spots.
Coatings add extra protection against corrosion. Some treatments strengthen the outer layer. A well-finished product lasts longer. It also performs better in harsh environments.
Optimizing Wall Thickness for Longevity
The right wall thickness prevents cracks and breaks. Thin walls reduce weight but may weaken the product. Thicker sections improve strength and stability.
Balanced thickness avoids stress points. Precision casting ensures even distribution. This prevents weak areas from forming. Stronger walls lead to a longer-lasting product.
Minimizing Porosity for Structural Integrity
Porosity weakens metal and shortens product life. Precision casting reduces air pockets in the material. This improves strength and prevents cracks. Controlled cooling helps avoid internal defects.
Proper techniques ensure even density. A solid structure withstands heavy loads. Fewer weak spots mean a more durable product.
Enhancing Heat Treatment Processes
Heat treatment makes metal stronger and tougher. It improves hardness and wear resistance. Controlled heating and cooling remove stress. This prevents warping and cracking over time.
Some methods increase flexibility without losing strength. Investment cast stainless steel is one example of a material that benefits from heat treatment. Proper heat processing extends product life.
Reducing Stress Points in the Design
Sharp corners and uneven shapes cause stress buildup. Precision casting allows for smoother transitions. Well-designed curves distribute pressure evenly. This reduces the risk of fractures.
Rounded edges prevent weak spots from forming. Balanced designs improve resistance to strain. Products last longer when stress is minimized.
Applying Protective Coatings for Longevity
Protective coatings shield metal from environmental damage. Special coatings prevent rust and corrosion. Heat-resistant coatings protect against high temperatures.
Some coatings add a layer of wear resistance. Precision casting allows even application of coatings. Proper coating methods extend product life. A well-coated product remains durable over time.
Ensuring Proper Quality Control Measures
Strict quality control prevents defects in cast products. Regular inspections catch flaws early. Testing methods check for strength and durability.
Precision casting allows for consistent quality in production. High standards ensure better performance. Careful monitoring reduces failure risks. Stronger products result from thorough quality control.
Enhance Product Durability with Precision Casting Techniques
Precision casting techniques improve product durability in many ways. They help select strong materials, refine surfaces, and create better designs. Proper thickness, reduced porosity, and heat treatment also play a role.
Stress-free structures increase longevity. These methods make products last longer and perform better. Industries benefit from using precision casting for strong and reliable components.
To read more, you can check our blog page. We do have more!